The American auto industry embraced automation as a way to reduce costs and improve quality, but also speed changes.
Japan was slower to embrace some of this thinking.
MODICON ( modular electronic controller ), is the brand we use the most up here in my industry.
You can trace the roots back to GM for the brand, they were developed in the late 60s to replace all those boards of relays.
As far as the quality of the workmanship I have seen wiring done in Canada and the USA done to very fine quality second to none.
Trouble is you have to be prepared to pay for it most places won’t!
First generation automation and systems were designed to last they were well made and repaired and programmed by the people who installed them at the plant so.
This looks like hell today but consider it old and in an unfriendly environment with no one coming to maintain it.
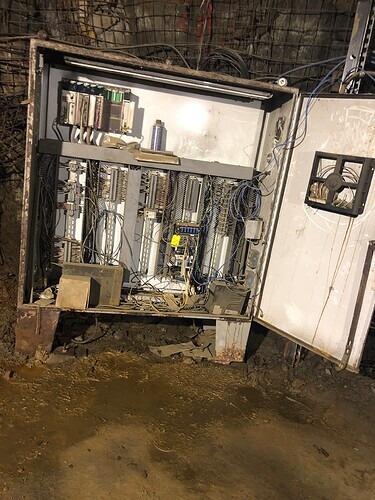
Time has marched on and it has been adapted to work with fibre and Ethernet rather than its native MB+ and copper cable.
Look real close at the encloser and you see a full length piano hinge that’s rotted away heavy steel construction that has not rotted throw, paint that did a good job of sticking and a rats nest of wires all cut open from what was once some very neat tidy and colour coded to function.
Brown was inputs and orange was outputs…
You have to want to pay for quality and then pay for people to keep it up.
If you don’t pay this is what you get ( sooner or later it will stop working )
Here’s the future.
You skip the PLC hub and use smarter starters that a central computer systems can monitor.
Make the processes simpler, bite sized and dummer to the point where the stater itself is all that is left.
Then the guys someplace else can run monitor and trouble shoot from a remote location.
Local people do not need to know whats going on or how to run it…
Its saves in labour costs, training and equipment.
All of these things can be made cheaper and disposable now.
Yes I do remember the big boards or relays though.
I could listen to the clicks and tell you what was going on above me on the floor.
And when it stopped I walk down the length of the big MCCs and logic boards and tap a hung relay pretty fast to restart everything.
A mean operator in a pullet someplace could make those relays do tricks and keep me running all night if he wanted ( maybe he did not know what he was tripping but he could learn the systems responses to his inputs and remember what went wrong last time and do it again )
A good operator could also tell you what was happening and speed up a break down.
Machines still suck at this ( but they break down less so I think its a wash ).
Time was you learned your plant, your equipment, the people you worked with and expectations of the bosses.
If you could find a common ground to work together then the plant hummed…
Japanese plants hummed a long real well because they were and still are better at this than we are.
We however have tried to and succeeded in making every mistrust each other to the point you cant hire people, don’t train people, don;t properly compensate or reward people, and we have no loyalty to your employer.
We had some visitors Sunday at the plant.
Our Manager ( an Engineer I respect and speak to often ) and the CEO… and every strata in between.
The people at the very top do not speak out language, and even if they did they still do not understand.
The manager is told what to do from above.
In the days before the information and data metrics flew around at the speed of light the manager might get a phone call from Toronto or NY and tell him what our numbers were, what was going on and what we needed and daily operations were in his hands.
Now I don’t expect him to be able to decide the colour of his shirt. ( in fact he has to wear a green one with the company logo on it ).
Still a nice guy though, but there is no decision he can make to really control the operation of the machine or help me with my task of maintaining it.
That’s why we don’t make things in this country anymore.
I mean we do but we make the cheapest simple things that don’t require pride or skill.
We have become the people that make the junk that they used to make in poor countries.
Ironic then that we see people in poor countries with higher levels of skills making things by hand with no machines at all.
Funny how I get off on a tangent and ramble…
Sorry