Carl suggested I document my experiences with nozzles in my Toyota Corolla gasifier, particularly to show my results with horizontal air entry versus vertical air entry to the reaction zone of the SimpleFire updraft-style charcoal gasifier.
The first photo shows the original side air inlet 1.5 inch stainless steel pipe nipple nozzle with a stainless steel sheet metal shield after about 20 miles. This pipe nipple was mounted horizontally. I replaced that with the Lettinger style nozzle shown in the same photo after it had been used for about 65 miles. This nozzle is made of a 1.5 x 12 inch schedule 80 steel pipe nipple used for steam applications. It screwed in place of the side entry nozzle, but functions as a vertical nozzle with the holes facing up toward the gas outlet at the top of the reactor.
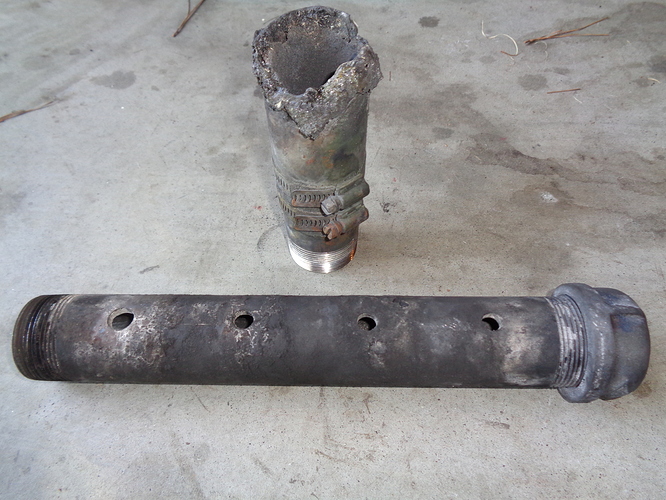
Below is a close-up of the Lettinger nozzle after 65 miles.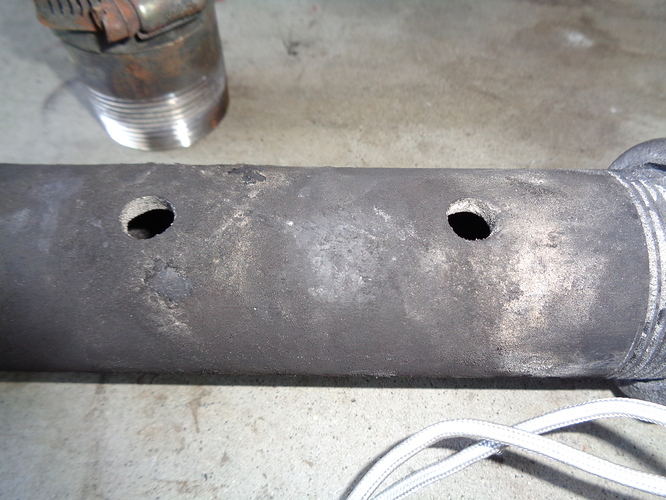
I had the holes drilled larger in the Lettinger nozzle and reinstalled it. Then after 128 more miles this is what it looked like:
I did not notice any deterioration. Here is a close up of it:
I had the “bright” idea of trying to lower my reaction zone by going back to a side entry nozzle similar to the first one, but with a one inch pipe and a heavy floor flange on the end to protect it. Here are two view of it before installation:
Here are two views of the results after only about 15 miles. The most deteriorated part was facing up toward the gas outlet with an accumulation of slag at the bottom.
Lesson learned for me: Unless there is some cooling method employed and/or material which can take the high heat, the side entry nozzle is not likely to last long in the updraft gasifier. the nozzle will fare better if the gas is taken off opposite the direction the air is entering the reaction zone. I have decided to stick with Kristijan Lettinger’s design.
Others have pointed out that the durability of Kristijan’s design is due to the mass of metal surrounding the holes and the accumulation of slag on top of the pipe forming a protective coating for the pipe which separates the pipe from the glowing charcoal.
One disadvantage with this nozzle design is that it is difficult to monitor the temperature by the color of the glowing charcoal, because you can’t see it clearly from the air inlet, but as Kristijan has pointed out, by examining the accumulation of slag vs. ash at clean-out time, you can determine whether it has been running too hot or cold and make the necessary adjustments for future operation. If I remember correctly, a lot of slag formation indicates a high heat situation. I remember the first time I removed the Lettinger nozzle, there was virtually no slag. The last time there was nearly an inch of slag formation on top of the nozzle. Hope this helps.