I have a lot of this stuff it’s pretty thick. I have metal to weld fins I think. I’d just be heavy. it’s not quite 2in inner diameter dose that matter? I have some bigger stuff that it fits in it’s probably 3in.
That is some really thick pipe. With the smaller pipe inside the larger pipe it would make some great flute nozzles for a gasifier.
I think I would look for some pipe that was half the thickness you have there.
Conduit pipe works good for hopper tubes I bet. It’s thick enough to weld reliably but thin enough to shed heat and not weigh too much.
My only worry with those drums is collapsing under the vacuum. I have had a couple straight wall drums for making charcoal and I closed the lid too tight, came back next day to see them collapsed.
Air nozzles? That would be awesome. Do you mean I could cut the big pipe into rings that the small pipe would fit in and maybe weld a washer or cap on the end of the small pipe so it can come out easier? Could I thread the washer or cap holes and add easy to unscrew tough nozzles?
I might be able to make metal rings from rebar or something to reinforce the inside of the smooth walled drums with a internal iron cage. I found some other drums but they aren’t the type that clip together but are flared. I could probably cut a hole in the top and bottom and join them together some way. I think I have some conduit pipe and galvanized post that might work for the hopper.
I’ll have to maybe share a few drawings I’ve done trying to figure out the scale of how big the Gasifier will be. Also how I’d like it to work. I have a idea for a removable internal baffle for the heat exchanger. Like I said in the beginning I wanted a clip together easy to dismantle unit. I’m still thinking about it.
The pipe would slide inside of the other pipe with holes drilled in it. This is for a flute nozzle design. Not to be confused with a firetube down draft design gasifier.
Trying to reinforce a smooth wall light metal barrel is difficult. My plastic smooth wall hayfilter has a tendency to collapse under the vaccum of the gasifier system when the engine 5.2 liter is drawing on it. 40 plus vaccum is a lot of vaccum. I have wooden discs inside the barrel with the hay to keep it from collapsing. Plastics are flexible stell is not , it will bend and not go back in to place. So strong rigged barrels are needed in a gasifier. The salvage or oil barrel with out side rings to make them rigged and strong are needed. The heavier gage steel is better.
It would be a shame to build a gasifier with all the hard work a have it collapse.
Well I might be able to get these other barrels they just don’t have a open top but I think I can make something work. I think the truck I have draws a lot of vacuum so I’d like to see it not collapse in.
I’d be nice to find some old well pressure tanks or 2ft wide propane tanks. Those would probably last forever.
Those should be perfect if they have a removable top.
Otherwise you’ll need to splice the tops from those other drums into the ribbed drums.
I’m using that type of barrel on 2 of my builds. Lots of ways to make them have top fill hatch.
And seal the two barrels together.
I have this big piece of well pipe I can use for the heat exchanger.
I was trying to figure out how it would work. I wanted to make a baffle that can be removed easily.
Greg since this is on a public side discussion it would be a good idea to remove the drawing.
Sorry. I didn’t realize
It’s alright, have you already bought the book? Once you get Premium Side access you can post WK gasifier related stuff on there.
I’m waiting to go to my uncle’s house that’s far away, I might be able to get a barrel for free there. I’m just waiting to buy the book until I have some barrels. I think I can manually flare the edge.
They have this fancy tool
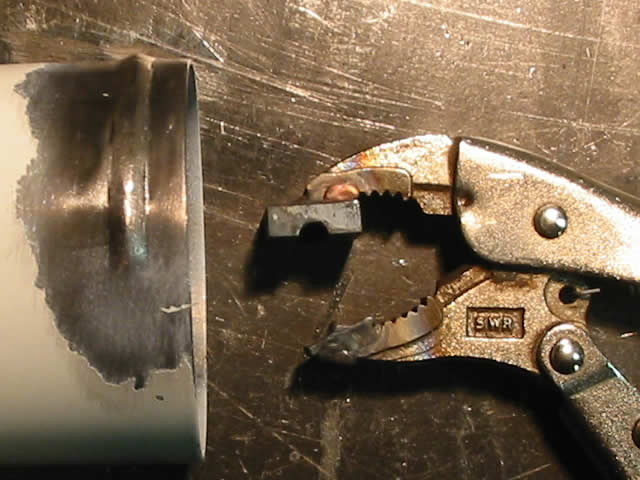
But I can also make my own maybe.
To be honest I’ve never needed one. I just butt weld it. You can get pipe vise grips made for butt weld joints.
Oh yeah you are right. I’d just need to cut a ring out of one of the barrels and and butt it against the bottom or top of another drum weld it then cut out a hole.