I’m losing a lot of gas out the air intake with each pulse. I’ve tried several different configurations of air control valves but they have all allowed gas to escape.
Any thoughts on minimizing gas loss through the intake?
Tuned runners?
Video trying to show the gas exiting the air valve.
https://youtu.be/oiZW1r-bXTE
You culd just extend the air supply pipe. That way the pulse will nor be able to push the gas the whole lengh of the pipe.
I am thinking of trying out a idea l had a while ago, makeng a membrane expansion vessel to use this action in to an advantige but lm not there yet…
I did do that but it took a really long pipe to work and it looked weird:) Also, it made for some really odd startup dynamics where large changes in air/gas mixture happened with changing rpm.
I currently have a removable pipe which I take off for startup. Kind of a hassle.
hello chuck, i have the secondary air intake after the gas filter immediately on my builds…will say immediately where the filtered gas comes out, so, because there is a longer hose between filters and engine intake , the gas has no time to escape…
further the rubber hose is protected more from heat because fresh air is mixed in,
the valve near the engine intake i use only for easier start, than, when engine runs good, i close this valve always a bit more while opening always a bit more the valve after gas filter…
look at my thread of the red bear mower, there is explained …and also pictures
Anyone remembering what thread we discussed this earlier?
I posted some sketch of a: “back-pulse damper” without moving parts.
I don’t know about the old thread but I built this manifold for my 14.5 hp 7.5 k generator a long time ago…have since got rid of the woodgas generator that was attached.with hoses…but was able to just adjust butterflies and run sizing your woodgas generator to your engine is the biggest thing…it is not a one size fits all process the WG generator I had for this was about size of a 5 gallon pail…with 1" air inlet…
Nice manifold build Dennis. Did you experience gas exiting the intake?
I’ve searched for the sketch you mention Goran but I haven’t found it yet.
I’ll move my mixer valve to near the course filter Giorgio. All that mass should dampen the pulses. The cooling effect is nice too.
I see MattR does the same (mixer far from the engine).
Do you think it will be more difficult to start with a more remote air inlet?
I think having the mixer further away is best for the carburetor. Matt has found that with the mixer assembly directly attached to the carb it adds weight and stresses out the bolt holes in the Head.
Made some new drawings, this is based on some common principles used in engine tuning, especially two-strokes. The “simple” one is the only that needs to be calculated “exactly”.
The others can be tested along. The expansion chamber along with the suddenly change from negative to positive pressure should do the work.
This “principles” can probably be incorporated, “built in” the gasmixer instead of building separately?
Red arrow’s show back-pulse
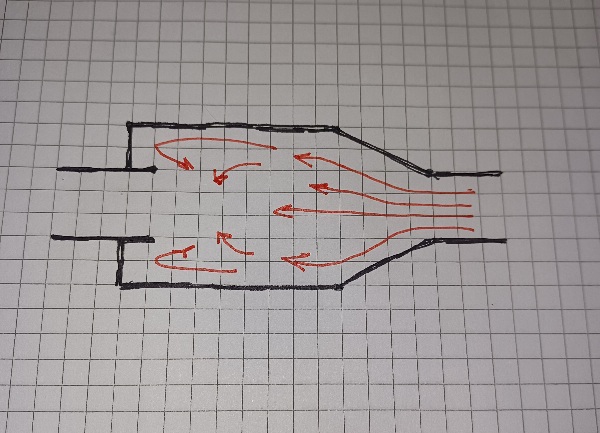
Just some ideas,
My manifold is made of EMT conduit and weighs less than air filter assembly have had this manifold on this engine for about 10 years without any issues…if it was any further away…I would support it some way. with my setup I could use my engine to pull the gas to carb by running on Gasoline and closing the air butterfly and when engine started running rich…use my toggle switch and shut fuel off at carb…and adjust my air and gas butterflies until I got the sweet spot. Just worked for me…
Hey Goran,
I did something very similar (or I thought I did) by using the filter box as the expansion chamber. Not enough volume I guess. If a larger air box volume would fix it that would be nice. Having the mixer valve near the engine controls makes sense to me.
Reminds me of the Tesla one way valve;
https://en.wikipedia.org/wiki/Tesla_valve
I’m talking more of people that add to the existing airboxes with PVC valves unsupported. I work with a lot of conduit and I agree your setup is definitely light enough.
Wow, that screams for a 3d printed part! How easy is that?
I would try putting a piece of corrugated plastic shop-vac hose in the system. It sure smoothed out air and gas flows for me.
Rindert
I thought I have seen a non-spring flapper type plumbing backflow preventer used in a video I saw a couple or three years ago? Seems like the pipe for the air mixing valve turned horizontal. It was several inches long, then the back flow preventer and then the mixing valve open to atmosphere
Is your air mixer located directly at the carb? If so you may want to set it up remotely, ever since I started doing this that issue went away.
Another thing is check your valve lash you may need to tighten it up.
Hey Matt,
I saw your setup and others have recommended it. Do you have any startup issues with the air valve so far from the engine?
Good tip on the intake valve. I had actually loosened it up and might have left it a bit too loose. Everything is so floppy in that valve train it’s a little hard to measure.
No not really. I just pull start to prime the gas with the valve closed. Then with the valve still closed I hit the electric start and they fire right up.
Actually if the valve lash is loose then the valve is closing plus some delay. So that should alleviate the pulsing.
An ecellant topic and good exhanges going on here on this problem.
Yep. I sucked a lot of single cylinder intake woodgas CO in the Victory Gasworks Shops 2009-2012.
My many reverse flow ideas did not work out so well. Internal reversal edge ledges and l-o-n-g intake pulse tuning piping led to RPM biasing. Means only works in a single narrow RPM range. And make the problem worse outside those ranges.
Long distance remote mixer mounting helps, yes. But then have slow response times. Can lead to extended long cranking engine starting up. Gives a lot of fuel-air volume for a significant intake valve ignited pop-boom.
All leading to my advice since: to just get 3-4 cylinder engines to not have the pulsating intakes.
And that will pull load your woodgasfier systems up hotter to perform better anyway.
Even two cylinder, and V-twin generator engines have pulsating intakes.
But now with my newest near 500cc single cylinder Inverter-Generator and back at the intake pulsating on woodgas.
This time I am approaching differently.
A loaded single cylinder engine has THREE pulsating sources.
Intake.
Crankcase.
Exhaust.
How are the different liquid gasoline carburetors systems using these for benefits?
Three of my seven fourstroke small engines use crankcase pulsator gasoline fuel pumps.
And some of these are using crankcase pulsations into the carb side of the air cleaner box to even out intake gasoline spitback.
And ALL of my current all-position 2-stike engines use crankcase pulsations in their carburetors to pump liquid mix into the carburetor.
You can see these three pulsations in slow motion on the Project Farm YouTube channel.
You can see very detailed engine pulsations for gasoline carburation benefits on the very detailed educational TheRepairSpecialist YouTube channel.
So . . . how do single cylinder propane mixers conversion kits meter and control low pressure suppled propane, eh? I only have worked with multi-cylinder propane mixers. Steady intake Flow volume metering. Some with exhaust O2 sensor feedback duty cycling solenoids.
I am just going to have to buy different single cylinder propane dispensers; open them up. and see. Diameter says they are using intake pulsations to meter propane gas…
Then how to upsize for a low pressure delivered woodgas?
Accommodate the soots in woodgas.
The corrosion of woodgas. Bronze. SS. Some plastics.
For now I only have unproven ideas.
For now . . . for me . . .for you-all; a simple in air cleaner housing mixer works good-enough.
Regards
Steve Unruh