Pepe, THAT is a great looking machine!
I have been getting puffbacks on mine from air leaks too. I don;t hardly flinch anymore. Most are from not emptying gas first or trapping oxy in start-up.Operator error. I have been experimenting with my adapter sleeve and getting anywhere from ‘less than good’ to GREAT! results. I’m learning the machine much better. I wish I had made mine more disassembly friendly like you have. Next one I will. good luck to you. Gordon
Hay Pepe; Where I have steel to steel flanges and I want to seal them I get a product from Manards
Be sure to read what it says. There are several that look just alike. The one I uses says good up to 1375 degrees. I don’t think it is flexible. It drys hard. I have to take a wire brush on a drill to clean the surface after use But, when you have bolted together flanges, it seals them very well.TomC
Pepe,
That’s interesting how some of it is still intact. Could it be possible that a small air leak developed where the two ends met together and just got worse with time? I remember at one time Steve U telling me that if one is going to use a gasket, to spend the money and get a continuous gasket. Of course he told me over a year ago, so I may be remembering it wrong. But I’m wondering if this is the reason? I also remember him telling you to put two rows in to balance it out.
While I agree with your other advice I would tack weld a nice fitting sleeve inside of the outgoing side of the gasifire before the joint until after the joint as a heat shield. I did this on my flanged crossovers but inside that I made a double walled insulated pipe as well. it is about 5/8" thick filled with mineral wool. It is ready to bring outside and crack off but I am waiting for temps to get up in the 20s so a guy can spend the day out there. Was looking for a pic but I need to get a new cord to upload them. Dam puppy but in his defence it is the only thing he has destroyed.
Hi Jim,
Thanks for commenting. I did mention a sleeve connection in my post above. I thought it would do just what you mention as a heat shield. Man, if it’s not one thing, it’s another chewing up the hours, lol. This is the first time that gasket has been destroyed. I think the shield fitting into the outgoing side is correct also. I will try it using the same gasket material also. The cyclone shroud is relatively easy to R & R.
Pepe
Hi Tom,
Thanks for the link. I found the 1375 degree F stuff. If my sleeve doesn’t work, I will give this stuff a try. I just remembered there is also a firestop material that we used on the NYC and LRR cars we built in Plattsburgh, NY. I’ll have to get some specs on it from my former QA team members. It was a red moldable material. Can’t remember if it eventually set up, though.
Pepe
Hi Bill,
Thanks for commenting. That’s what I love about this site, there are many folks jumping in to help. I think that’s exactly what happened and I agree that a single piece gasket would be ideal. I’m hoping the firestop I mentioned above will fit the bill along with the sleeve. I had added the double gasket and Steve noted the added advantage of equal pressure to keep the joint tight.
Pepe
Thanks for the update. I haven’t taken a long look at the site yet, but I will.
Pepe, I used stove rope and the 2000° adhesive that came with it from Menard’s. I worked the adhesive into the rope first let it dry a little then slight even pressure when I assembled to let it dry. After it had time to dry is when I snugged it up. Seemed to work.
Hey Gordon,
Thanks for the compliment. It’s been almost 2 years getting to this point! I went back and reread your blog looking for clues to performance. Your post on 12-30-2014 @ 0945 hrs reminded me of my post on 12-28-2014 @ 1347 hrs. Your firetube diameter is also your “nozzle ring” diameter. As a beginner “slicing and dicing” 100 lb propane tanks I had yet to start considering fuel flow. Pic 1, I just joined some “stuff” together and the 2 ridges inside the tanks provided a hangup spot for fuel, first bad. Pic 2 further down the the curve of the tank provided a “shelf” for further hang up possibilities just before the firetube entry. We seem to have similar “hang ups”. Pic 3 shows my nozzle protrusion necessary to get my nozzle diameter to the “imbert” specs on the chart. My firetube is 9 3/4" diam. I followed the chart because I didn’t know where I was going really. Smaller fuel and Dan Cox’s hopper vibrator seems to have resolved the bridging problem for me. Hope Murphy didn’t hear me say that!
And of course, my biggest hangup, ungasketed drop in hearths, etc. This is the only performance issue I could see, internal leak lets gas bypass the reduction zone diluting your gas.quality. Some will poopah this, I say why chance it… Your hearth diam and height above the restriction are almost 1 to 1 which I believe is close to a standard ratio, so that’s good, imho. Smaller fuel is a definite must considering the ledges,etc. I’m presuming you’re making a separate drop in with flange for your different numbers trials. Let me suggest that you layout a hole pattern on the flange for bolting the flange down using a suitable gasket material. I would look for a flat wood stove type gasket wide enough to put your bolts through. Double it up spacing the joint 180 degrees. I’ll try to find a source for the flat gasket material.
Drill the flange holes, drop in the unit and using the drill, mark the locations. Don’t drill the same size hole, these holes will be tapped and require a different size bit. This should eliminate that joint as a source of “internal” leaks. Nick a reference mark on the flange and the mounting base for quick and easy line up of parts. Make a full size pattern of the bolt pattern and use it on all new flanges. Insert your drop in and mark the hole locations where the drop in will go. Drill and tap these holes. Now your new trial flanges will have the same locations to bolt to. Don’t forget to reference these flanges to the original index marks.
First pic is the beginning of my slice and dice trip on propane tanks. These are still parts of my present gasifier! I thought you would appreciate the design changes I’ve been through.
Steady as she goes, Mate.
Pepe
Thanks everyone for your comments, every little bit helps.
I’m going to install the top end of my cooler tubes on an angle to match the hopper lid. I figure the gas is being deflected in that direction why have it change directions again and create turbulence. Again, every little bit helps. They will be 3" wide, 2" deep and 16" from tip to tip. I’m working on the area, will post later.
Pepe
OK, it’s later. The area of a trapezoid is (base 1 + base 2)/2 x height
The area per tube is approx. 1.25 sq ft. Adding 4 tubes will add 6 sq ft. or approx 37% increase in surface area. 6 tubes approx 47 % increase. More than likely I’ll use 4 tubes.
EDIT I erred, 4 tubes is only 5 sq ft or approx 31.25 % increase.
The initial area of my monorator is 16 sq ft.
Hi Pepe, You are very observant…I was having air leaks and diluted gas from a non-gasketed adapter “drop-in” hearth. I like your idea about securing it with bolts. I wasn’t getting accurate results so I just pulled the adapter out and put dropped my original choke 2-3/8" in. I ran some hardwood trim pieces ‘smaller’ and was amazed at the quality of the gas! I didn’t have to shake the machine to cure bridging and overall flow was great.I killed my flare and put a paper towel over gas for 30 secs and had no soot to speak of. I had full conversion going as far as I could tell…very little filtering. Very hot exothermic burn inside and gas exiting was very cool going into the dropbox.
I have been doing other things around the house and haven’t been working on the machine for a week…argh! I will update soon Gordon
Ps. Amazing how similar our builds are.
Hey Gordon,
Every time I re-watch a video I seem to find another nugget. I’m talking moisture. Are you still running the gas to the filter first? Somebody may have already noted this, but if not. I think it would be advantageous to run the gas to the cooler first, wring as much moisture out of it as possible before sending it to the filter. The tar in your filter is on its way to the valves. You’re correct on the not cracking tars, heat relationship. Definitely been there on that one.
I have an idea where you have to only drill one set of holes in the mounting base and bolt on a “clip” to hold down the new flange. Just keep the flange the same OD on your experiments. I also show how I added my airtight ignition port, yours may be a different size. Next time I will make mine bigger, minimum 1" clear opening for easier lighting. Have fun.
Pepe
EDIT I would make the hold down clip 1" wide, not 1/2".
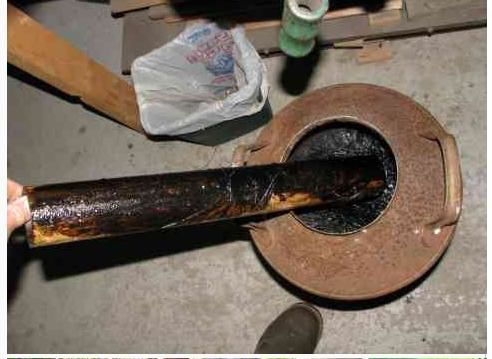
Hi pepe,
I have my hot air going straight into my drop box which acts like a cyclone. It is dry now. I had a problem with tar and water on my first fireup because I was running that wet green Madrone wood and I was not cracking the tar at all hardly. I had lousy suction too. I actually think running straight into my dropbox cyclone is the way to go because I have massive cooling in there. On a WK design there is a heat exchanger in the dropbox. The action in the dropbox slows the draw so much that the soot just falls to the bottom. I also have 4 " of stainless steel scrubbers near the top that really help alot. There is also some fiberglass insulation,but I am going to put that after the cooler now. I just have to open the lid and hose it out or pull the stainless and wash it. Very easy and fast cleanup. Air exiting the dropbox to cooler is around 120 to 200 degrees depending on how hard I'm running it. Total dry soot powder in the bottom of the dropbox and in stainless scrubbers. Air going into dropbox is around 350 to 550 depending. I think this is because I am getting a good endothermic reaction before the grate. I 'm still learning. Gordon huh forbidden ...forbidden
Hey Pepe how did that bouncehouse blower work for you. There is one on Craigslist for $30 right now. Should I but it? I need more air now so I can see what she’ll really do. Gordon
Hi Gordon,
Now I know what the drop box is and what it can do. Guess I’d better bone up on the WK a little bit. Yes, my only concern was the water, but it looks like you’re on top of it, great. I haven’t yet used the Bouncehouse blower. It is 120v, 60hz, 4 amp, 480 watts.No stated rpm. I got it at a garage sale for $8. It seems to put out a pretty forceful blast of air, but I’ll see how many inches of water it pulls when I get a test set up later this week. It is an all plastic housing.
I tried posting this with the other cooling tube pics above, but it wouldn’t work. ??? This is a full size print applying the test of reasonableness. It should fit perfectly. The top angle is the slope of the lid. The gas is going that direction, let it flow! The moisture from the tubes empties directly into the monorator hopper moat. Yes, it’s worth the hassle of the build for me to ascertain if it’s a worthwhile change so others can make build decisions. I don’t like the tight weld underneath the top tube, but I think I can reach it OK. That’s one of those reasonableness assessments made easier with a full size drawing. I’ll cut this apart for laying out on my metal plates, then cut and weld. This will be good thin metal welding practice as it is 16 gauge heating oil tank. Believe it or not the pencil is more powerful than the cutting torch, ask the French. Long live the freedom of speech and God bless America! Ok, I’ll put the soapbox away, but not my 16. figuratively speaking, of course
Pepe
That should look nice on that BIG ole hopper you got! Are you going to put rubber boots in it for cleaning? That machine is really nice. Gordon
That should look nice on that BIG ole hopper you got! Are you going to put rubber boots in it for cleaning? That machine is really nice. I’m picking up that blower tomorrow. I need to work with more air sometimes for my testing. Thanks for all your thoughts and concerns about my machine. I could not be this far if not for the help and comments and overall discussions on this site. God bless you and everyone here. I 'm nervous about this cheap oil…somethings going to happen and for once I’m totally baffled. I have my thoughts but…? Gordon
Hi Gordon,
Yes, everyone on this site is helpful and courteous. This group can’t be beat. As for the thank yous, you’ll get to return the favors by helping someone else. One hand washes the other. We help each other learn. I can’t wait to get started on the cooling tubes. I’ll be cutting out parts tomorrow. I got called to one of our rentals in Tupper Lake today, reconnect a crawl space heater unit. I think the hopper is going to look real neat. Gordon, I thought about clean outs and then I opened my lid and there’s plenty of room to reach the tubes with a high pressure hose. Wash everything into the moat, then remove the screwed on plates from the hopper and “rake” it clean so to speak. God bless back to you, man.
Pepe
EDIT: This oil thing has me quite suspicious, too…
Hello Fellow woodgas enthusiasts,
Took some time to transfer the plan to cardboard, cut out some parts and do a layout. Then I did a mock up of the top transition duct. Time consuming, but it proves the fit. It will take me 8 to 12 hrs to complete the addition.
Pepe
EDIT: In the second pic the narrow piece (#4 on bottom left) missing and in pic #3 part #5 (on bottom left) shown will both be left out and covered by the 7 1/4" straight tube section joining the 2 end transition pieces.